How the Most Expensive Swords in the World Are Made
Summary
TLDRThe video script offers an in-depth look into the centuries-old tradition of crafting Japanese swords, renowned for their exceptional strength and sharpness. It details the meticulous process from gathering iron sand to mastering the art of sword-making, highlighting the Tatara method for steel production and the importance of carbon content in determining the blade's hardness and flexibility. The script also touches on the cultural significance of these swords, their high value, and the artistry involved in their creation, emphasizing the dedication and skill required to produce such cultural artifacts.
Takeaways
- 🗡️ The method of crafting traditional Japanese swords has remained virtually unchanged for centuries, highlighting the enduring skill and craftsmanship involved.
- 🏹 Japanese swords, specifically those made using the Tatara method, are renowned for their exceptional quality and can sell for as high as $105 million.
- 🌊 The process of making steel in Japan starts with gathering iron sand from rivers, which is concentrated through a method of river diversions and filtering.
- 🔥 Iron sand is smelted at high temperatures using charcoal in a process that requires careful control and continuous monitoring.
- 🔧 The steel produced is then sorted by quality and carbon content, a skill that is tested as part of becoming a certified swordsmith.
- 🔨 Swords are forged by hammering and folding the steel, which not only distributes impurities but also creates a unique grain pattern in the metal.
- 🗣️ The carbon content of different parts of the blade is manipulated to achieve the desired balance of hardness and flexibility.
- 🛡️ Quenching the blade in water after covering it with clay forms different types of steel (ferrite and martensite) which gives the sword its strength and iconic curve.
- 🔍 The final polishing and sharpening of the sword is a meticulous process that can take up to a month to complete by hand.
- 🎓 Learning to use a Japanese sword involves extensive training, even for seemingly simple tasks like drawing and sheathing the blade.
- 🎨 Japanese swords are not only weapons but also considered works of art, reflecting the deep care, attention to detail, and love for the craft by their makers.
Q & A
What is the significance of the Japanese swords mentioned in the video?
-The Japanese swords mentioned in the video are renowned for their exceptional strength and sharpness, capable of slicing a bullet in half. They are considered among the best in the world and have been crafted using methods virtually unchanged for hundreds of years.
How did the Japanese gather iron sand for sword making?
-The Japanese gathered iron sand by utilizing the natural process of river sedimentation. They noticed that iron oxides, being denser than other minerals, would accumulate in places where rivers changed direction or speed. They amplified this effect by creating diversions in rivers to increase the concentration of iron, resulting in iron sands with up to 80% iron oxides by weight.
What is the Tatara method and why is it significant in Japanese sword making?
-The Tatara method is an ancient technique of steelmaking, used only in Japan. It involves a smelting process that has remained virtually unchanged for over 1300 years. The steel produced by this method, known for its high quality, is used exclusively in the making of the finest Japanese swords.
How did the Japanese sword makers shift from bronze to steel?
-Japanese sword makers shifted from bronze to steel about 1200 years ago during the Heian period. Bronze, an alloy of copper and tin, could be sharpened but was too soft to hold an edge for long. Steel, an alloy of iron and carbon, provided a stronger and more durable material for sword making.
What is the role of carbon in the steel used for Japanese swords?
-Carbon plays a crucial role in determining the hardness and rigidity of the steel used for Japanese swords. High carbon content makes the steel hard and capable of maintaining a sharp edge, which is used for the blade's edge. Lower carbon content is used for the spine, allowing for flexibility and preventing the sword from breaking during combat.
How does the process of folding steel affect the quality and structure of a Japanese sword?
-Folding steel spreads out impurities throughout the steel, ensuring a uniform consistency without weak points. It also creates a grain in the steel, reinforcing it in the direction it will be hit in combat. The folding process can create beautiful patterns known as hamon, which is the edge pattern visible in a finished sword.
What is the purpose of the quenching process in sword making?
-Quenching is the process of rapidly cooling the heated sword in water. This process, influenced by the different thicknesses of clay applied to the blade and spine, creates varying steel structures - martensite for the hard edge and perlite for the flexible spine. It also results in the iconic curve of a samurai sword.
How long does it typically take to sharpen and polish a Japanese sword?
-Polishing and sharpening a Japanese sword is a meticulous process that can take up to a month. It is done by hand using whetstones of different coarsenesses to achieve the desired sharpness and finish.
What is the significance of the hamon in a Japanese sword?
-The hamon, or edge pattern, is a visual indication of the different steel structures formed during the quenching process. It represents the combination of soft and hard steel (ferrite and martensite) and is a sign of the sword's quality and the skill of the swordsmith.
What is the importance of the swordsmith's role in the creation of a Japanese sword?
-The swordsmith plays a critical role in the creation of a Japanese sword, from selecting and sorting the steel by quality and carbon content to forging, folding, and shaping the sword. Their expertise and craftsmanship determine the sword's functionality, durability, and aesthetic beauty.
How does the video emphasize the value of craftsmanship in the making of Japanese swords?
-The video highlights the meticulous attention to detail, the extensive skill, and the time-honored traditions involved in every step of sword making. It underscores the value of craftsmanship as not only a means to create high-quality artifacts but also as an expression of art and cultural heritage.
Outlines
🗡️ The Art of Japanese Sword Making
This paragraph introduces the topic of Japanese sword making, highlighting the incredible strength and sharpness of these swords, which can slice a bullet in half. It emphasizes the unique access granted for filming the entire process, from gathering iron sand to the final use of the sword. The discussion points out that the method of making these swords has remained largely unchanged for centuries, and they are still regarded as some of the best in the world. The paragraph also mentions the high value of these swords, with one from the 16th century appraised at $105 million, making it the most expensive sword ever. The setting is established with a description of the Tatara method of steel making, which is an ancient technique still practiced in Japan today.
🏞️ The Origins of Japanese Sword Materials
This section delves into the history and origins of the materials used in Japanese sword making. It explains how the early swords were made of bronze, an alloy of copper and tin, but were later replaced by steel due to its superior properties. The narrative then explores the geological history of iron, from its abundance in the oceans to its deposition in sedimentary rocks known as banded iron formations. The paragraph also discusses Japan's unique geological challenges in obtaining iron, given its volcanic geology and lack of sedimentary iron oxides, leading to a late start in steel production compared to other civilizations.
🔥 The Traditional Smelting Process
This paragraph describes the traditional Japanese smelting process, focusing on the Tatara method. It explains how iron oxides are collected from river sands and then smelted at high temperatures to produce pure iron. The process of turning iron into steel is detailed, highlighting the addition of carbon from charcoal to create the strong alloy. The paragraph also discusses the physical and chemical processes involved in smelting, including the removal of impurities and the creation of slag. The narrative follows the smelting process over a 24-hour period, culminating in the production of a 100 kg block of steel, iron, and slag, from which only a third is of high enough quality for sword making.
🔨 The Forging and Tempering of the Sword
This section focuses on the forging and tempering of the Japanese sword. It explains how the steel is sorted by quality and carbon content, which is crucial for the different parts of the sword. The process of folding the steel to distribute impurities and create a grain is described, along with the use of different carbon percentages for the edge and spine of the blade. The paragraph details the hammering process, the use of clay for quenching to create different steel properties in the edge and spine, and the resulting curvature of the sword. It also touches on the high failure rate during the quenching process and the subsequent tempering to reduce brittleness.
🔍 Polishing, Sharpening, and the Legacy of Sword Making
This paragraph discusses the final stages of sword making, including polishing and sharpening, which are done by hand with whetstones. It emphasizes the time-consuming nature of these processes, with a single sword taking up to a month to complete. The paragraph also explores the cultural and artistic aspects of Japanese swords, including engravings and the historical significance of sword making. A personal account of learning to use a katana from a master is shared, highlighting the deep respect and tradition associated with these weapons. The paragraph concludes with a reflection on the artistry and craftsmanship involved in sword making, drawing parallels with other high-quality creations and the importance of dedication and love for one's craft.
🎥 Behind the Scenes of the Video Production
This final paragraph provides a behind-the-scenes look at the video production process, thanking the sponsors and collaborators involved. It mentions the support from Henson Shaving, who are compared to the Japanese sword makers in terms of their dedication to quality and craftsmanship in their razors. The paragraph includes a promotional offer for Henson Shaving products and expresses gratitude to the viewers for their interest and support of the content.
Mindmap
Keywords
💡Japanese Swords
💡Smelting
💡Forging
💡Tempering
💡Quenching
💡Hamon
💡Carbon Content
💡Tatara Method
💡Swordsmith
💡Cyanobacteria
💡Martensite
Highlights
Japanese swords are renowned for their strength and sharpness, capable of slicing a bullet in half.
The method of crafting these swords has remained virtually unchanged for centuries, with everything done by hand.
Japanese swords represent the pinnacle of weapon craftsmanship for their style of warfare and available materials.
A 16th-century Japanese sword was appraised at $105 million, making it the most expensive sword ever built.
The Tatara method, used for smelting steel, is an ancient technique still practiced in Japan today.
Sword making in Japan dates back 3000 years, initially using bronze which was later replaced by steel due to its superior properties.
Iron is obtained from iron sands, which are concentrated through a process involving river diversions.
The process of smelting iron involves heating iron oxides to over 1250 degrees Celsius to obtain pure iron.
Charcoal, used as a heat source, is key in the creation of steel by adding carbon to iron.
The steel produced is sorted by quality and carbon content, a skill required to become a certified swordsmith.
Folding steel spreads out impurities and creates a grain, resulting in a uniform and reinforced material.
Different carbon percentages are used in different parts of the blade to balance hardness and flexibility.
The iconic curve of a samurai sword comes from the formation of martensite during the quenching process.
Polishing and sharpening a sword is a meticulous process that can take up to a month to complete.
Learning to use a Japanese sword involves extensive practice, even for simple tasks like drawing and sheathing the blade.
Japanese swords are considered not only weapons but also works of art, reflecting the deep care and expertise of their makers.
The video emphasizes the importance of doing any craft with deep care, attention to detail, and love for the work.
Transcripts
- [Derek] This is a video
about how Japanese swords are made,
swords that are strong enough and sharp enough
to slice a bullet in half.
The access we got for this video is incredible.
We were able to film everything from gathering the iron sand
to smelting the iron, forging the sword,
to sharpening and polishing it.
They even let us use it.
- [Petr] That is so cool!
- [Derek] The method of making these swords
has remained virtually unchanged for hundreds of years,
with everything done by hand.
They are still considered to be among the best in the world.
- The Japanese made a weapon
that was the absolute pinnacle for their style of warfare
and the materials they had at hand.
- These swords are held in such high regard
that one from the 16th century
has been appraised at $105 million,
making it the most expensive sword ever built.
(sword thwacks) (dramatic music)
(river noises)
In the Shimane province of Japan
there is a smelter that is lit for only one night each year
where steel is made in the same way it was 1300 years ago.
It's known as the Tatara method,
and only steel made in this way ends up
in the very best Japanese swords.
And we were invited to come film it.
(drums and flute music)
Just after 9:00 AM, the ceremonial prayers are said
and the fire is lit by a Shinto priest.
Everyone that will be working this smelter will be here
for at least the next 24 hours.
That includes Veritasium producer Petr.
- I'm committed. We're gonna do this.
It's gonna be fun.
- [Derek] Sword making in Japan goes back about 3000 years,
but in those days, swords were made out of bronze.
We're not sure how people first learned to smelt metal,
but it was likely related to pottery.
- In that you were using these rocky oars
to make glazes and such for pottery
under very controlled atmospheres.
And then find maybe the potters found metallic beads
in the bottom of the furnaces that they were firing it.
This possibly gave them the idea.
- [Derek] Bronze was discovered before steel
because it's an alloy of copper, and usually tin,
both metals with low enough melting points
that they can be smelted in regular pottery kilns.
The problem with bronze
is that although it can be sharpened,
it's too soft to hold an edge for long.
So Japanese sword makers shifted to steel 1200 years ago
in the Heian period.
This is what most people would recognize
as a Japanese sword.
It's made of steel with a curved blade.
Steel is an alloy of iron,
the fourth-most-common element in Earth's crust.
The oceans of the world used to be rich with dissolved iron.
But two and a half billion years ago,
cyanobacteria started photosynthesizing and creating oxygen.
The iron reacted with that oxygen
precipitating out of solution
to be deposited at the bottom of the ocean.
Incidentally, the cyanobacteria were poisoned by the oxygen
that they themselves produced
so it's thought that when levels got high enough,
they died off, and as a result, oxygen levels dropped
and iron no longer precipitated out of solution.
Then the cyanobacteria could multiply again
and the cycle repeated.
That's why most of the world's iron is found in layers
of sedimentary rock called banded iron formations.
Each layer of iron was formed
during a global flourishing of cyanobacteria
that infused the ocean with oxygen.
The majority of the global iron supply
comes from these banded iron formations
because of their high concentration of iron,
up to around 60% iron oxide by weight.
(gentle music)
But Japan, with its mostly volcanic geology,
has barely any of these sedimentary iron oxides.
And this is likely why the country was late
to the steel production game.
Archeologists have found steel artifacts in Anatolia,
which is modern day Turkey, that are nearly 4,000 years old.
But in Japan, metals including steel,
were imported from China and Korea
up until the eighth century
when Japan started making its own steel.
So where did they get the raw ingredients?
Well, igneous rocks like granite and diorite
still contain iron oxides,
just in much lower concentrations.
But as the mountains are weathered,
these iron oxides are broken apart and washed downstream.
Eventually they become part of the sand.
The Japanese noticed that because iron oxides
are denser than other minerals in the sand,
they accumulate in places
where the river changes direction or speed.
The heavier iron sinks to the bottom
and the lighter material is washed away.
To amplify this effect,
they deliberately created diversions in the river
to increase the concentration of iron.
- What do you do is you dam off a section of river
and then you drag sand into it.
Because iron is heavier than the other parts of the sand,
it is the thing that gets left behind
and everything else gets washed downstream.
- [Derek] With this method, you can get iron sands
with 80% iron oxides by weight.
That's more concentrated than high-quality iron ore.
And since it has fewer impurities,
it's an excellent source for high-quality steel.
If you heat up those iron oxides
to over 1,250 degrees Celsius,
you can break the bonds with oxygen and get pure iron.
But pure iron is actually softer than bronze.
So in its elemental state, iron provides no advantage.
But nature gave humans a lucky break.
One of the few ways you can heat something up
to 1,250 degrees is with charcoal,
and charcoal is basically pure carbon,
and if you add just a little bit of carbon to iron,
it creates an incredibly strong alloy: steel.
- Yeah, a lot of people see it as a heat process.
I see it as a chemical process.
- [Derek] Alloys are usually stronger than pure metals
because they contain different sized atoms,
and this reduces the ability of atoms
to slide past each other when an external force is applied.
- So I've just been given gloves, other gloves, and a towel.
So things are very much getting real.
I'm genuinely quite worried.
(serious music)
Here is the room with all of the charcoal
that we're going to be using overnight.
There's just bags and bags of this stuff.
(charcoal rattles)
(flame crackles)
There's a Buddhist saying:
"Before enlightenment, chop wood, carry water.
After enlightenment, chop wood, carry water."
So we're lining up on the four corners, I guess.
(charcoal rattles)
Oh. Oh boy.
Didn't do a great job of that. (chuckles)
(thunder rumbles)
So the rain is coming,
so we're quickly getting all of the charcoal out
and then measuring it.
So each bag of these is 10 kilos. Okay.
(serious music)
So with the iron sand, it is mixed together with water
because if you don't mix it with water
and you put it on the flame, it just flies straight up.
But if you mix it with too much water,
then there is water that's gonna heat up.
It's gonna become water vapor,
and the whole kiln could explode.
Terrifyingly enough, they do this by feel.
They mix in enough water until the iron sand is clumpy.
But again, if it's too much, the whole thing could explode.
Okay, put some iron in.
It is just past four in the afternoon,
and over the last couple of hours
we have added 250 kilograms of charcoal
and nearly 60 kilograms of iron sand.
So yeah, it's a slow process,
but I think we're starting to get somewhere.
I have no idea because obviously the thing is hidden,
but it should be growing.
- [Derek] To achieve the high temperatures
required to make steel,
you need a strong, steady supply of oxygen.
For hundreds of years,
this was provided by huge foot-operated bellows.
It would've taken an around-the-clock, full-body effort
by many men to maintain the furnace's temperature.
- When I came here,
I was a little bit sad that the bellows were electric.
I really wanted to, you know, have this proper experience,
have this proper workout
of stepping on these bellows for 24 hours.
(serious music)
- [Derek] The temperature inside the smelter
gets up to 1500 degrees Celsius,
just below the melting point of iron, which is 1538 Celsius.
So the iron being smelted isn't liquid,
but it's soft and malleable enough
to clump together into a big block of iron.
No matter how high quality the iron sand is,
there will always be some impurities,
like sulfur, phosphorus, and silicon oxides.
They combine with carbon from the charcoal
and melt at a lower temperature than iron,
so they become liquid and flow to the bottom.
This is known as slag.
After many more hours of adding charcoal and iron sand,
it is time for the first removal of the slag.
Before the first removal of slag, another prayer is said.
(steelworkers clap)
- Oh, that's insane.
(slag sizzles)
(serious music)
(hammer pinging)
Whoa.
So for the last three hours,
there's been three processes that we've been doing.
One is adding the charcoal, two is adding the iron sand,
and three is opening up the smelter from the bottom
to break apart the impurities so they can flow out.
(shovels scrape)
Just want you guys to know that it's 3:16 in the morning
and I'm still here and I'm really sleepy.
(subdued music)
So it's currently six o'clock in the morning the next day.
We've been smelting for 21 hours.
I'm exhausted, but the sun is about to come out
and it's been pretty amazing, I gotta be honest.
We gotta close these doors really quick
before they get mad at me.
- [Derek] At 9:00 AM the next morning,
the smelting is complete.
A total of 614 kilograms of iron sand
and 670 kilograms of charcoal were added to the smelter.
At this point, in a traditional smelter,
the only way to get the steel out
would be to break it apart.
These days, a crane is used
to take the smelter apart.
- [Petr] Oh wow, okay.
Oh!
- [Derek] And what is left to show for all that hard work
is a 100 kilogram block of steel, iron, and slag.
Only around a third of this block is high enough quality
to be used in sword making.
(crane whirs and clunks)
- Oh, that's insane. That's so cool.
The result for all the hard work.
This is step one of making a Japanese sword.
(subdued music)
- [Derek] The steel is sorted by quality and carbon content,
which is also done by eye,
in fact, this is one of the exams you need to pass
to be certified as a swordsmith.
Then, the different grades of steel are sent out
to one of 300 swordsmiths around the country.
Only 30 do it as their full-time job,
and one of them is Akihara Kokaji,
who we went to visit next.
This is when the forging of the sword begins.
In a coal oven with hand-pumped bellows,
the steel is heated until it is soft and malleable.
Then using hammers,
the master swordsmith flattens out the steel.
In the old days, this would've been done by the swordsmith
and three apprentices.
The swordsmith using a smaller hammer, would set the rhythm
and the apprentices would use big mallets
to flatten the steel.
(hammers clank) (Petr grunts)
- Woo. That was terrifying.
- [Derek] These days, electric hammers are used.
When the steel is flat enough,
it is then bent back on itself,
(fire crackles)
and it is then hammered again
to press the steel back together into a solid block.
(gentle music)
So why go to all this effort flattening the steel,
only to fold it back on itself
and end up with a chunk of steel the same size as before?
Well, because folding does two very important things.
First, it spreads out the impurities
like silicon, sulfur, and phosphorus.
It spreads them out throughout the steel.
This ensures a uniform consistency without any weak points.
Second, it gives the steel a grain.
After folding the sword, it is now reinforced
in the direction that it will be hit in combat,
and as a bonus, the steel is exposed to the air.
So there is a small amount
of oxidation creating a darker colored steel,
which when folded makes beautiful patterns.
There are some swords which have more than a billion layers.
Now this doesn't mean the sword
has been folded a billion times
since every fold doubles the number of layers,
so you only need about 30 folds to get a billion layers.
But usually a sword is folded 10 to 13 times,
resulting in a few thousand layers of steel.
Now a blade isn't made from a single block of steel.
The carbon content affects how hard the steel is.
So different carbon percentages
are used in different parts of the blade.
Because carbon atoms are much smaller than iron atoms,
they can fit inside the crystal lattice of iron.
These trapped carbon atoms
then apply an outward force to the lattice
putting the steel under stress.
The higher the carbon percentage,
the harder and more rigid the steel.
But this hardness comes at a cost.
The steel becomes brittle,
making it more likely to chip and shatter rather than bend.
So what swordsmiths do
is they use steel with different carbon contents
for different parts of the blade.
The edge is always high carbon steel
to make it hard and rigid
so it can maintain a sharp edge for a long time.
But the spine is usually made of lower-carbon steel,
which allows the sword to flex without breaking.
This is done by welding together pieces of steel
with different carbon contents.
- So we have about a 15-minute break
because you know it takes a while for the iron
to heat up and then meld together,
and then we're back in there.
It's very hot. It's very, very hot in there.
It's kind of unbelievable
that he can do this for four hours at a time.
- [Derek] After the sword is hammered into shape,
which is a straight blade, it is covered in a layer of clay,
a thick layer for the spine,
and a thin layer for the blade itself.
It's then heated in the furnace
and then rapidly cooled in water,
a process known as quenching.
Now, because the layers of clay have different thicknesses,
the rate of cooling is faster for the edge than the spine.
When the steel is heated, carbon enters the iron lattice,
and since the spine of the sword is covered in thick clay,
it will cool slowly,
giving time for the carbon atoms to leave the iron matrix.
This will lead to a very low-carbon steel called ferrite,
but the carbon atoms which have left the matrix
will be caught by other iron atoms
and created a type of steel known as cementite.
The combination of ferrite and cementite
is known as perlite,
and it's a mostly soft and ductile form of steel,
though parts of it are hard due to the cementite.
So per light forms the spine of the sword.
In contrast, the very thin layer of clay on the blade
means that it cools very rapidly,
so more of the carbon is trapped in the lattice.
This forces the lattice structure
to change from cubic to tetragonal
making a form of steel known as martensite.
Since the trapped carbon puts stress on the lattice,
martensite is incredibly hard,
exactly what you'd want for the edge of a sword.
The tetragonal lattice structure of martensite
also takes up more space
so the edge of the blade expands relative to the spine,
curving the sword backwards.
The iconic curve of a samurai sword
comes from the formation of martensite.
You can actually see the boundary
between different types of steel in a finished sword
by the difference in color.
This is known as hamon, which literally means edge pattern.
- At the Victoria Albert Museum in London,
there is a Japanese sword
that has a very detailed little dragon in the hamon,
and I've looked at it many times.
I don't, okay, I don't know how he did that. (laughs)
- [Derek] About one third of all blades
shatter during the quenching process.
- You quench it once
and you thank the stars that you made it.
- [Derek] The sword is then placed back in the forage
to evaporate any remaining water.
This also provides a little bit of energy
to loosen some of the crystal structures
making the sword less brittle.
- And that's about the extent
of the tempering process on a Japanese sword,
which that that might be enough to relax things a bit,
but they kept the edge much harder
than you would've in the West.
- [Derek] After the sword is forged,
it is sent to a polisher.
The polishing and sharpening of a sword
is also done by hand
with whetstones of different coarsenesses.
It can take a month to sharpen and polish a single sword.
- One of the things that I love is that like,
this table is sloping down
and the entire floor over there is sloping down.
So when you like add the water,
all of the residue and all the water,
you know, flows downhill so it's not perfectly flat.
(hammer taps softly)
- [Derek] Sometimes the swords
are also engraved with beautiful patterns,
though this is quite rare.
And after all that, the sword is done.
To learn how to use a Japanese sword,
Petr got a lesson from a master, Takara Takanashi.
He is the 10th-generation student
of Miyamoto Musashi, a legendary samurai.
Musashi killed his first opponent in single combat
at the age of 13.
He spent the rest of his life perfecting his sword-fighting,
inventing a new technique with two swords.
Musashi fought in more than 60 duels to the death,
and he won every last one of them.
(serious music)
(subdued music)
There is a story about a duel
that took place during a snowstorm.
As he faced his opponent, katana outstretched,
Musashi was so calm and kept his sword so still
that snowflakes began to accumulate
on the thin edge of the blade.
- [Petr] So during the lesson,
I thought I would get to use a katana,
but instead we spent the entire time
learning how to take the blade out of its sheath
and then put it back in.
So when I actually got the chance to use a katana
to slice through some things, I was deeply unprepared.
(katana thuds)
(playful music)
- [Producer] Well, it looks like it's your turn.
I'm so scared.
Okay, so this has been an amazing day.
We've looked at some beautiful katanas,
and now these wonderful people are letting me use one
of their just unbelievably beautiful pieces of art
to chop some things.
(Petr exhales forcefully)
(katana thuds) - Oh.
Oh.
- Woo!
Like this is kind of the best day ever.
(subdued music)
- [Derek] There really is something remarkable
about Japanese swords.
The amount of care, attention, and expertise
that each step requires,
from the gathering and refining of the iron sand
to the smelting,
to the forging and sharpening a sword,
each step takes so much time and skill.
It's incredible that all these things were discovered
by trial and error to produce artifacts of such high quality
that they are still prized centuries later.
(steelworkers speaking Japanese)
(steelworkers clap)
- [Derek] Before I made this video,
I didn't really appreciate
that swords can be art.
To me, it's a good reminder that whatever you do,
you should do it with deep care, attention to detail,
and love for the craft.
(both speaking Japanese)
- Do that enough times
and you might just make something beautiful.
(audio chimes and warbles)
Hey, this part of the video
was brought to you by Henson Shaving.
You know, making high quality things is hard,
and as far as I'm concerned,
Henson make the highest-quality razors in the world,
the katanas of the shaving world, if you will.
I've been using their AL-13 razor for the last year,
and it's the best razor I've used by a long margin.
One of the reasons for that
is Henson really understands the physics of shaving,
because as aerospace machinists for 20 years,
they understand how to cut things effectively.
They get precision.
Human hair is much harder than the skin it's growing out of,
and as a result, typical razors drag
and pull on the hair while cutting.
What a multi-blade razor does is it assumes
that the first cut will be ineffective,
and so they build in extra blades to cut the hair
before it can snap back into position.
And that does result in a good cut,
but it also increases friction
leading to razor burn and skin irritation.
Henson carefully studied that problem
and realized that you didn't need to add extra blades,
you just needed to properly support a single blade.
Virtually every razor on allows
for too much play in the blade, but Henson doesn't.
The result is an effective cut
without the additional friction on your skin.
Seriously, a Henson is truly a great razor.
It'll last you a lifetime.
You will get a better shave with less irritation,
and you'll also save money in the long run.
So head over to hensonshaving.com/veritasium
or scan the QR code here
and enter code "veritasium" for a hundred free blades
with a purchase of any razor.
I wanna thank Henson Shaving for supporting Veritasium,
and I wanna thank you for watching.
5.0 / 5 (0 votes)

Is he Cooked? Akademiks calls Myron from @Fedreacts to Breakdown Diddy’s Mansions Raids!

Valyrian steel: who has the swords that can defeat white walkers?
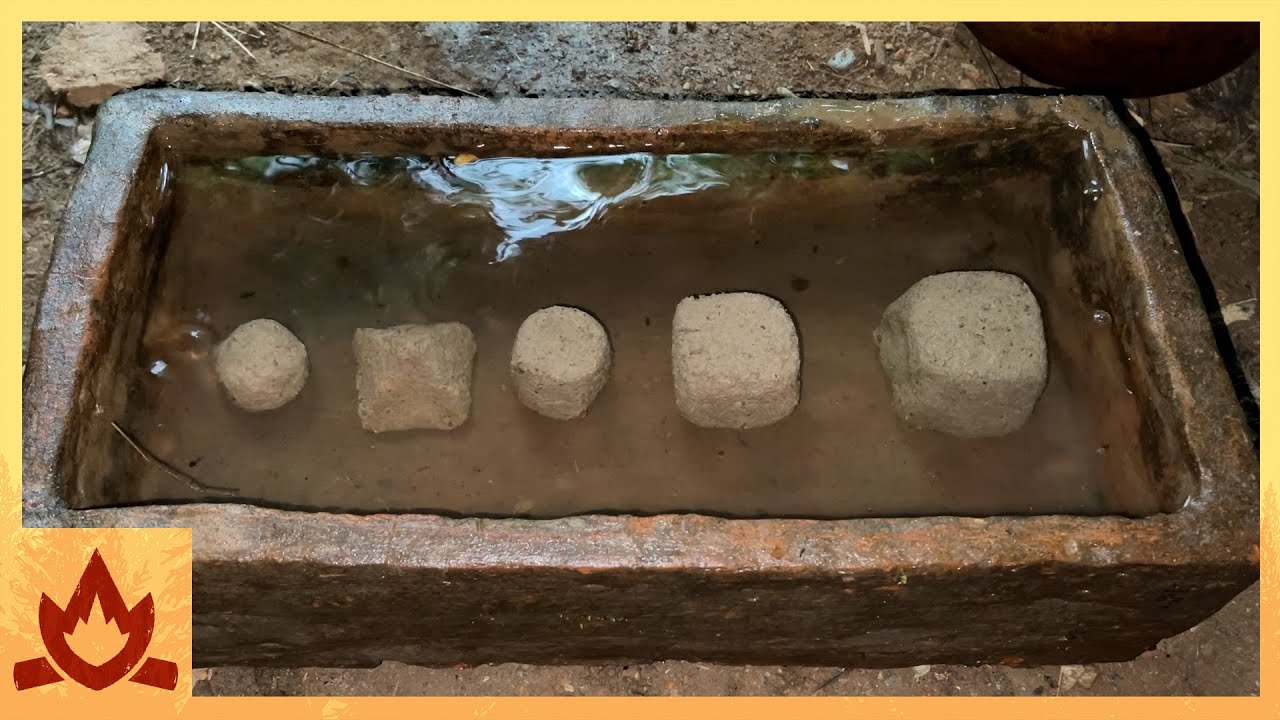
Primitive Technology: Geopolymer Cement (Ash and Clay)
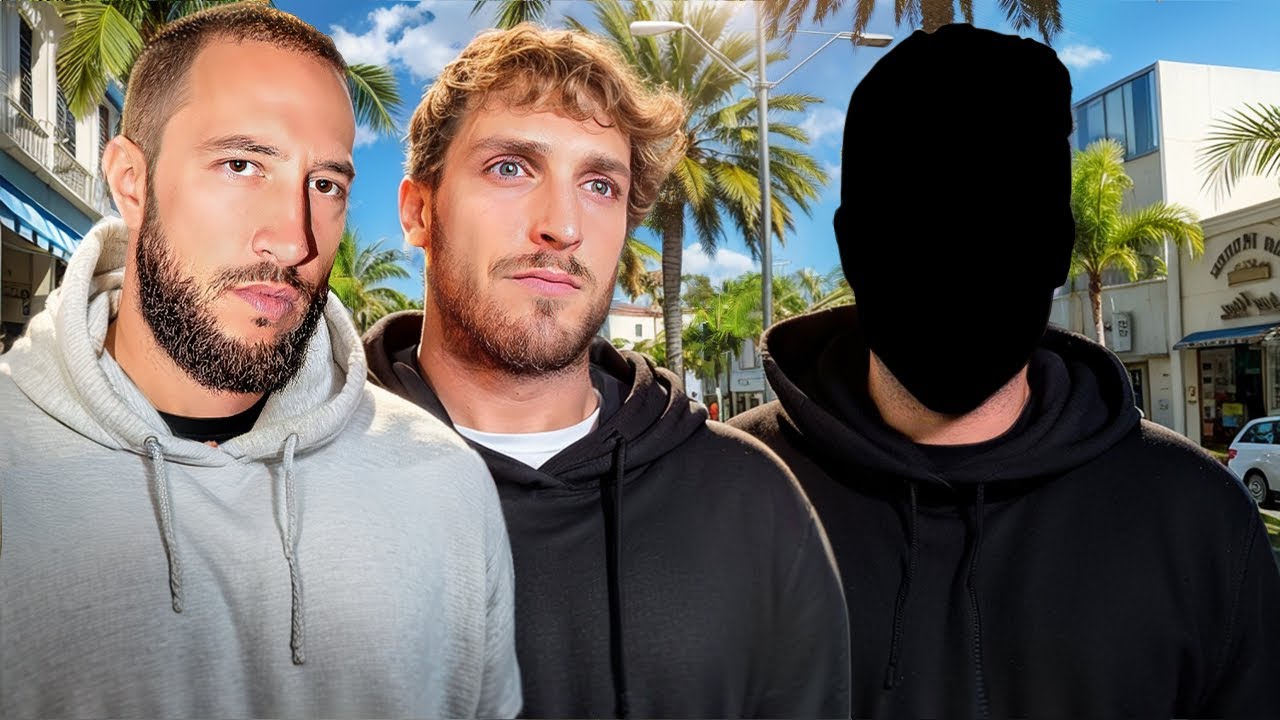
We Finally Confronted Our Old Friend… | The Night Shift
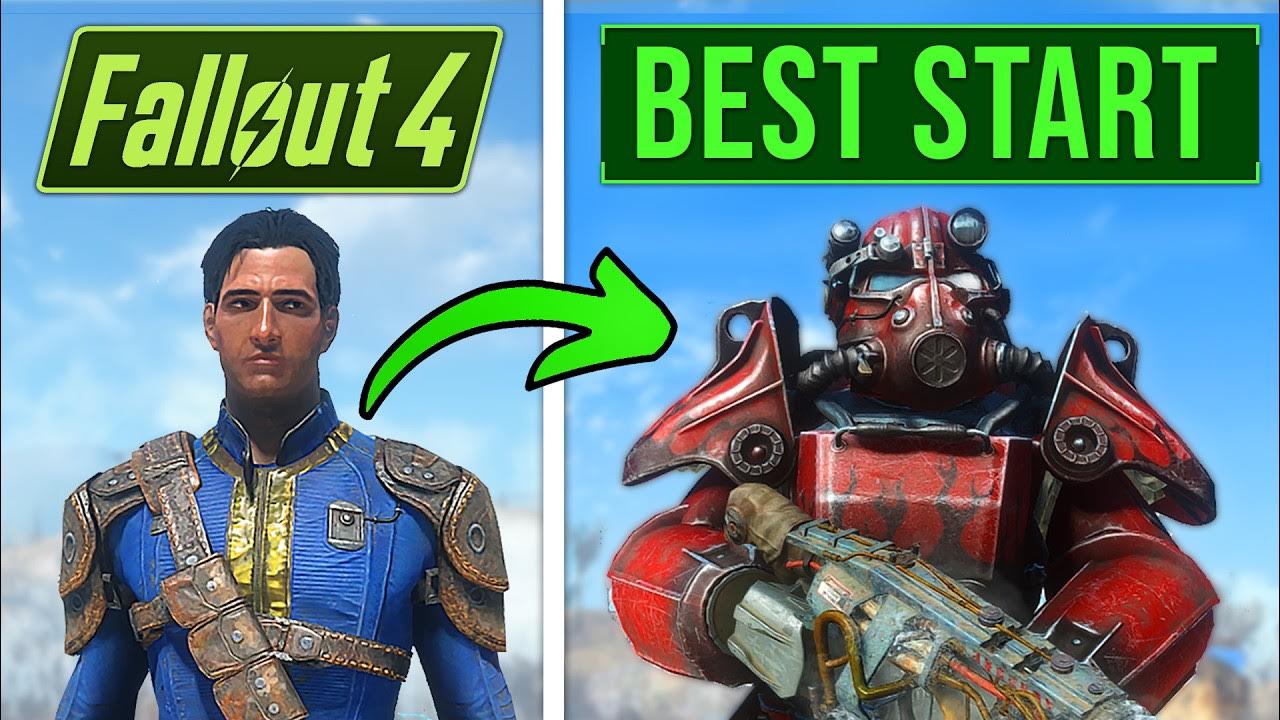
Don't Miss the Best Start in Fallout 4 - Next Gen Update!
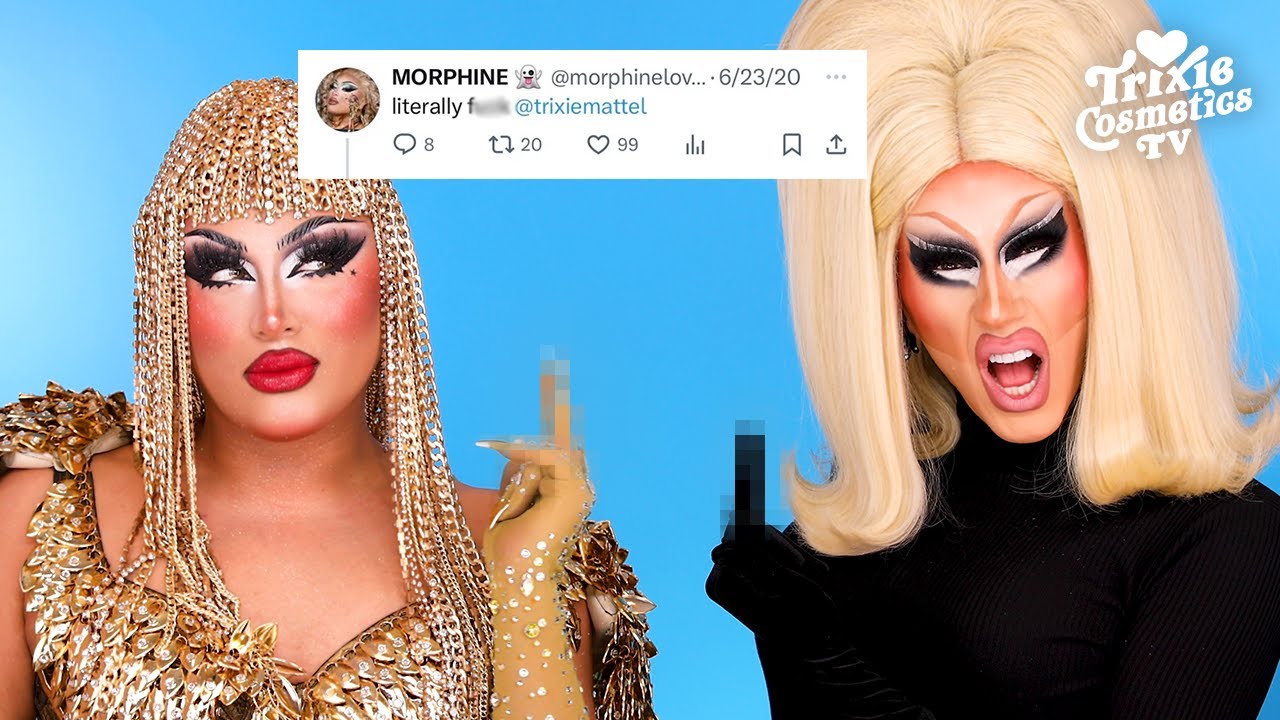
Addressing the Drama | Kiki with Morphine Love Dion