FreeCAD - Mesh Regions for a Better Analysis |JOKO ENGINEERING|
Summary
TLDRThis insightful video tutorial delves into the advantages and intricacies of meshing specific regions in FreeCAD to enhance analysis performance, paralleling experiences with SolidWorks. The presenter emphasizes how targeted meshing can dramatically reduce unnecessary computational effort while retaining desired resolution, especially in curved areas. Starting from scratch, the tutorial covers the creation of a basic 3D model, applying a directional force, and executing a G mesh analysis. The focus then shifts to demonstrating how creating mesh regions for specific faces can optimize processing time and improve analysis accuracy. This approach not only accelerates the meshing process but also offers a sharper resolution where it's most needed, showcasing practical visualization comparisons to underline the benefits of regional meshing in CAD design analysis.
Takeaways
- 😀 FreeCAD's ability to perform meshing analysis can significantly improve performance and provide useful results.
- 📊 Meshing in CAD software like FreeCAD, SolidWorks, Creo, or CATIA involves exponential processing scale, affecting analysis time and computational load.
- 🌍 Specifying only specific regions for meshing can save substantial processing power while maintaining desired resolution, especially for curved areas.
- 🖥️ In FreeCAD, using the part design workbench on the XY plane allows for the creation of detailed geometrical shapes like rectangles with symmetric constraints.
- 🔧 Applying directional forces at angles in FreeCAD helps define the parameters for the Finite Element Analysis (FEA) workbench.
- 📈 Precise meshing control, such as setting maximum mesh sizes, can optimize processing time and enhance the analysis's detail and accuracy.
- 🛠️ Utilizing sub-mesh regions in FreeCAD can provide higher resolution where needed without excessive processing, showing a smoother transition from small to default mesh size.
- 📐 Fixed geometries and applied forces in FreeCAD can simulate real-world conditions, aiding in a more accurate analysis.
- 🔍 High-resolution meshing in targeted areas leads to better stress distribution and more accurate stress concentration identification in the analysis.
- 📉 Visual comparisons in FreeCAD show the benefits of regional meshing for clearer and more detailed stress visualization.
Q & A
What is the primary focus of the video?
-The video focuses on the benefits and effects of meshing a region while performing an analysis in FreeCAD, a 3D parametric modeling software.
Why is meshing important in CAD software?
-Meshing is important because it helps in analyzing the performance of a design under various conditions, such as stress or displacement. It allows for a more accurate approximation of the physical behavior of the model.
How does the scale of meshing affect processing power?
-The scale of meshing has an exponential impact on processing power. A finer, tighter mesh will require significantly more processing power and analysis time compared to a coarser mesh.
What is the advantage of specifying a region for meshing?
-Specifying a region for meshing allows for targeted analysis, saving unnecessary processing power while still achieving the desired resolution in critical areas.
How does the video demonstrate the process of meshing?
-The video demonstrates the process of meshing by creating a simple rectangular model in FreeCAD, applying a symmetric constraint, and then meshing the model with different settings to show the effects on resolution and processing time.
What is the significance of the curved surface meshing in the analysis?
-Meshing a curved surface fundamentally involves approximation. The video shows that by using a sub-mesh region, one can achieve higher resolution in specific areas without significantly increasing the overall processing time.
How does the video compare the results of a standard mesh with a regional mesh?
-The video uses visualization tools to compare the standard mesh, which has a uniform resolution throughout, with the regional mesh, which has higher resolution on specific faces. The comparison shows that the regional mesh provides a better approximation and more detailed results, especially in areas of high stress.
What is the practical application of the insights gained from the video?
-The insights gained from the video can help engineers and designers optimize their CAD models for analysis, focusing computational resources on areas that require higher resolution, thus improving the efficiency and accuracy of their simulations.
How does the video address the issue of stress concentration in the model?
-The video suggests that by adding a higher resolution mesh to areas where stress concentration is observed, one can better understand and potentially mitigate the effects of stress concentration on the model's performance.
What resources are provided for further exploration of the topic?
-The video provides a link to a GrabCAD file where viewers can download and explore the meshed model further, allowing them to apply and test the concepts learned from the video.
Outlines
🛠 Meshing Analysis in FreeCAD and Its Benefits
This segment introduces meshing in FreeCAD, comparing it to SolidWorks to highlight the exponential nature of mesh processing across various CAD software. The narrator explains the process of creating a simple model and setting up a mesh analysis from scratch, emphasizing the importance of meshing specific regions to save processing power without sacrificing resolution, especially for curved surfaces. The process involves creating a model on the Part Design workbench, applying constraints, and using Gmesh for meshing. Despite a mesh error, the focus remains on demonstrating efficient meshing techniques to reduce processing time while maintaining high resolution in crucial areas.
🔍 Enhancing Mesh Resolution and Analysis Efficiency
In this part, the narrator continues with the FreeCAD demonstration by introducing a sub-mesh region to increase mesh resolution on a specific face of the model while keeping the rest of the mesh at default size. This technique is shown to significantly improve meshing speed and computational efficiency. Following this, fixed geometry and forces are applied to the model, and materials are specified for the analysis. The result set, displaying absolute displacement, demonstrates the advantage of targeted high-resolution meshing. Visual comparisons between general and regional meshing underscore better stress visualization and analysis accuracy. The video concludes by encouraging viewers to subscribe, promising more insightful content.
Mindmap
Keywords
💡Meshing
💡FreeCAD
💡Exponential Processing
💡Part Design Workbench
💡Gmsh
💡Curved Surface Approximation
💡Mesh Region
💡FEA (Finite Element Analysis)
💡Computational Power
💡Stress Concentration
Highlights
Introduction to meshing benefits and effects in FreeCAD, demonstrating its significant utility for analysis.
Comparison of meshing in FreeCAD with other CAD software like SolidWorks, CATIA, and Creo, emphasizing the exponential nature of mesh processing.
Explanation of the importance of specifying specific regions for meshing to conserve processing power while maintaining desired resolution.
Step-by-step guide to creating a basic model in FreeCAD using the Part Design workbench on the XY plane.
Demonstration of adding a directional force at an angle in FreeCAD for analysis purposes.
Introduction to the FEA (Finite Element Analysis) workbench in FreeCAD and starting a new analysis with a default mesh.
Troubleshooting a mesh error and proceeding with the analysis without delays.
Detailed explanation of meshing on curved surfaces and the need for approximation.
Using a sub mesh region to increase mesh resolution on a specific face while keeping processing time low.
Visual comparison of standard meshing vs. using a mesh region for higher resolution where needed.
Applying fixed geometry and forces in the analysis to simulate real-world conditions.
Discussion on material specification in the analysis, using steel as an example.
Presentation of analysis results, focusing on the improved resolution and computational efficiency achieved through regional meshing.
Visualization of stress distribution and the impact of higher mesh resolution on understanding stress concentration areas.
Encouragement to explore further by providing a link to download the FreeCAD file used in the demonstration.
Transcripts
in this video let's go over the benefits
and effects of meshing a region while
doing an analysis in free cab
this surprised me I learned that freecad
was able to do this it's a very very
event thing and it's very very useful I
will show some footage here hopefully
remember to edited of doing a quick
meshing analysis in SolidWorks this was
a video to help improve the performance
of SolidWorks and the findings are
meshes and meshing related processing is
really exponential in scale this should
not be a surprise and this should also
apply to freecad processing mesh is
going to be exponential no matter how
you slice it it doesn't matter if you're
in creo SolidWorks CATIA you know freak
adding anything will have an exponential
scale when processing you mesh that
means if I go to do a tight mesh in my
analysis I'm gonna take exponentially
more processing so if we can only
specify a specific region to mesh we can
save a whole lot of unnecessary
processing power and still get the
resolution we're looking for this is
particularly true for curved regions so
why don't we get started and I'm gonna
go do this from scratch so you can
follow along if you prefer and the part
design workbench on the XY plane I can
make a rectangle I can add and what my
background makes things kind of visible
so let me change it my preferences to
display colors color gradient apply and
we'll use the symmetric constraint to
make sure that we are centered here and
I'm going to use a shift H for a
horizontal dimension we're going to go
three inches wide shift V for a vertical
and two inches tall and we're going to
do that did not go to the center like I
will intended grab those two and combine
those points shift R for radius
quarter inch radius seventy-five clothes
will pad it's one inch tall so there is
a model I want to add a directional
force like I've done in the last video
this time we'll do it at an angle so it
takes three points to define a plane so
plane to find I can sketch on this and
we'll do something like in fact I'll
import this corner and I'll do something
like a four angle we can establish now
you listen like twenty five degrees
I'll make this four inches close that
and hide my plane so let's go back to
the FAA workbench and from here I'll add
in some basic constraints I'll start a
new analysis and we'll run a G mesh I'm
going to simply apply a default mesh but
and that did not seem to work I forgot
one thing
unless actually do this I'm going to
highlight my body or my pad here and now
say G mesh and now it's made a match
that's a that's a lot better we have a
measure era
fortunately I'm going to keep on going
so you can see the rest without any
delay so there's our standard mesh but
this is a curved surface and meshing
across the curved surface fundamentally
means approximation you need to
approximate if it's a curved surface so
one of the options for meshes is I can
of course say the same woman at my mesh
to be a maximum size of 50,000 remesh
this and you can see it's taking time to
calculate this in free cab to calculate
a 50,000 that
you know just a lot more processing and
when I go to run the analysis it's going
to be a lot more analysis time so we
we're finally done we have a small
mesh and that's you know that's one way
to do it but that just took a long time
so what I'm going to do is let my pad
gene match we're going to mesh at a
regular amount and now if I highlight my
mesh here I had the option for creating
a mesh region so I can add a face and
choose all the mesh on that face is
going to be 50 sow in inches okay so
I've added this sort of sub mesh region
if I show my mesh nothing has changed
right but now that I have this sub mesh
region I can double click and say apply
and now we're meshing at fifty thousand
space and a default measure there where
else and you can see that the mesh goes
from small back to its default size
quite smoothly this gives us more
resolution where we care about having
more resolution but we've mesh much
faster than faster than last time and we
have still a reasonable amount of
computational power it's a way that we
can get the resolution we want without
going up that exponential curve I can
finish this study out I'll hide this
mesh and start adding a few things maybe
I can add in some fixed geometry here
and I'll add in a force acting on this
face let's go with let's go with that
and make this nine fifty or some number
like that well specify a direction and a
reference to this face reverse it
all right so that's our analysis thus
far in fact you know what
instead of this face let's do this
the circular face here putting the face
on where we have a lot of that
definition now I can specify material I
like calculate steel we're doing
imaginary examples okay and it looks
like we're ready to run so I actually
don't quickly calculates all right the
InP
run calculates all right so we've got a
result set and you can see if I do my
absolute displacement I can hide this
body we have a very high resolution of
computation on our round face and our
smooth flat faces that probably don't
require as much are less so does this
bias anything are we better off with a
machining region then with the generic
machinist so how much let's do a little
bit of visual visualization with this so
first off I will take a look at some
images that I've compiled so if I use
the pipeline visualization tool and
freecad there you can see on the left
without using regional mission there's
default mesh all the way through and
basically what we've made on the right
and you can download this file from my
grab CAD and the link in the description
if you want to check it out further we
have much better definition especially
looking at stress down here the stress
appears to go much higher than with a
higher resolution it sounds like you
have a better approximation and scaling
as well so that's strength and if we
take a look at a result mesh you know
higher definition this looks actually
quite similar
but when you come down to stress you can
see we have a far different scale of
stress and you can see what you think of
as a large stress being dispersed across
his face is really a stress
concentration at this face right so
having a higher resolution on this face
would be a great argument for adding a
measure to disperse the stress like a
fill it where is this it appears the
stress is going a lot more through the
face and this is just what they look
like displaced and that looks quite
somewhere between the two pictures so
you can't get a lot better visualization
results through this looks like I'm
already past 10 minutes so I'm going to
call this video hope this video is
helpful if it was please subscribe and
I'll see you
[Music]
4.8 / 5 (43 votes)
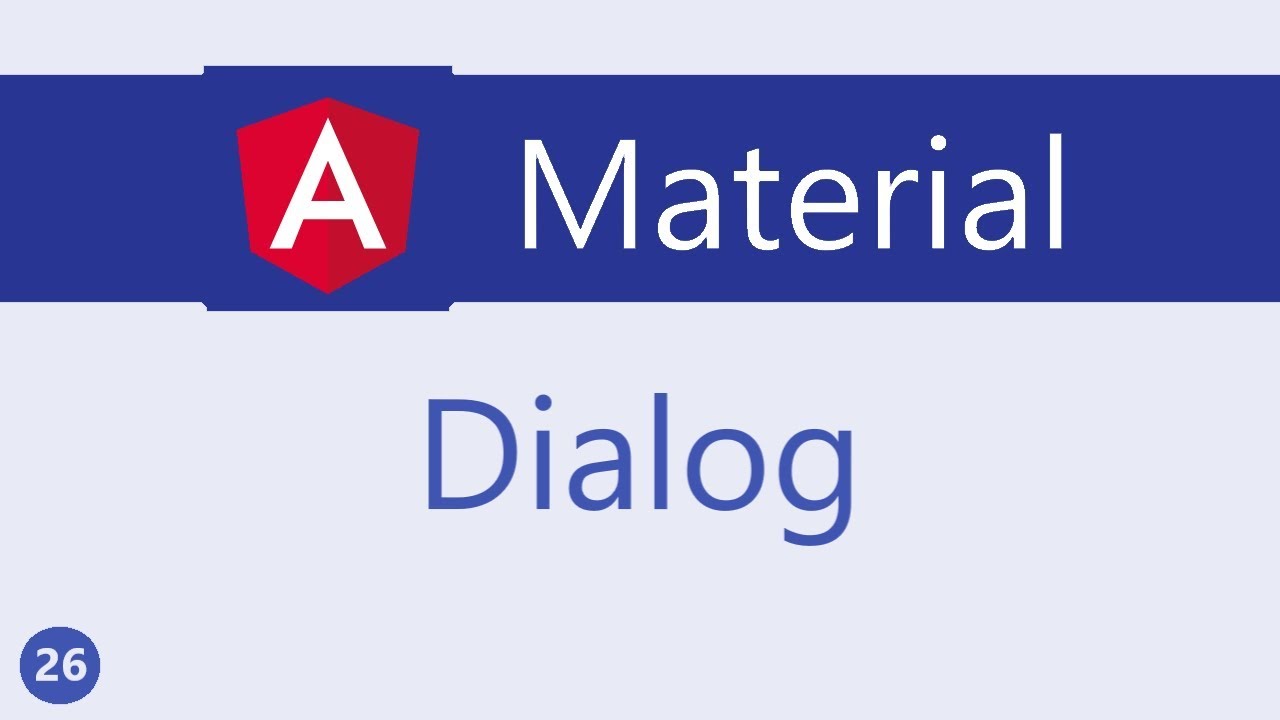
Angular Material Tutorial - 26 - Dialog
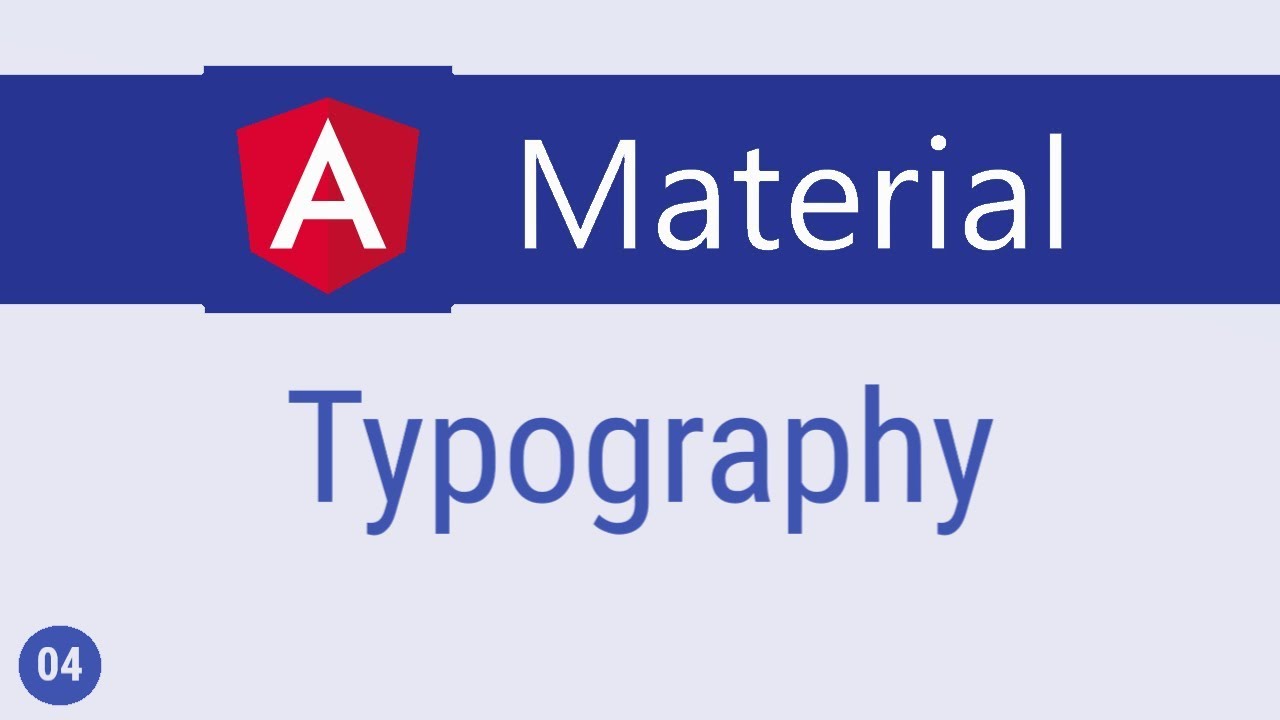
Angular Material Tutorial - 4 - Typography
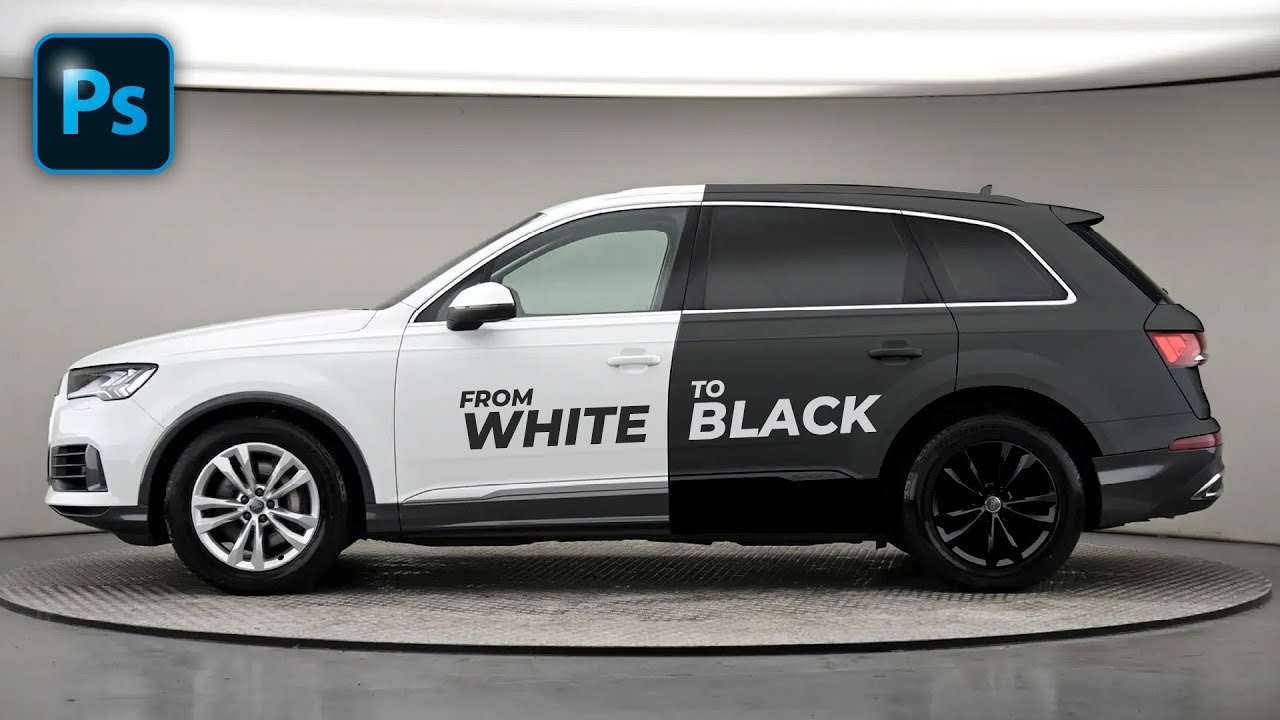
How To Turn WHITE Into BLACK Using Photoshop CC
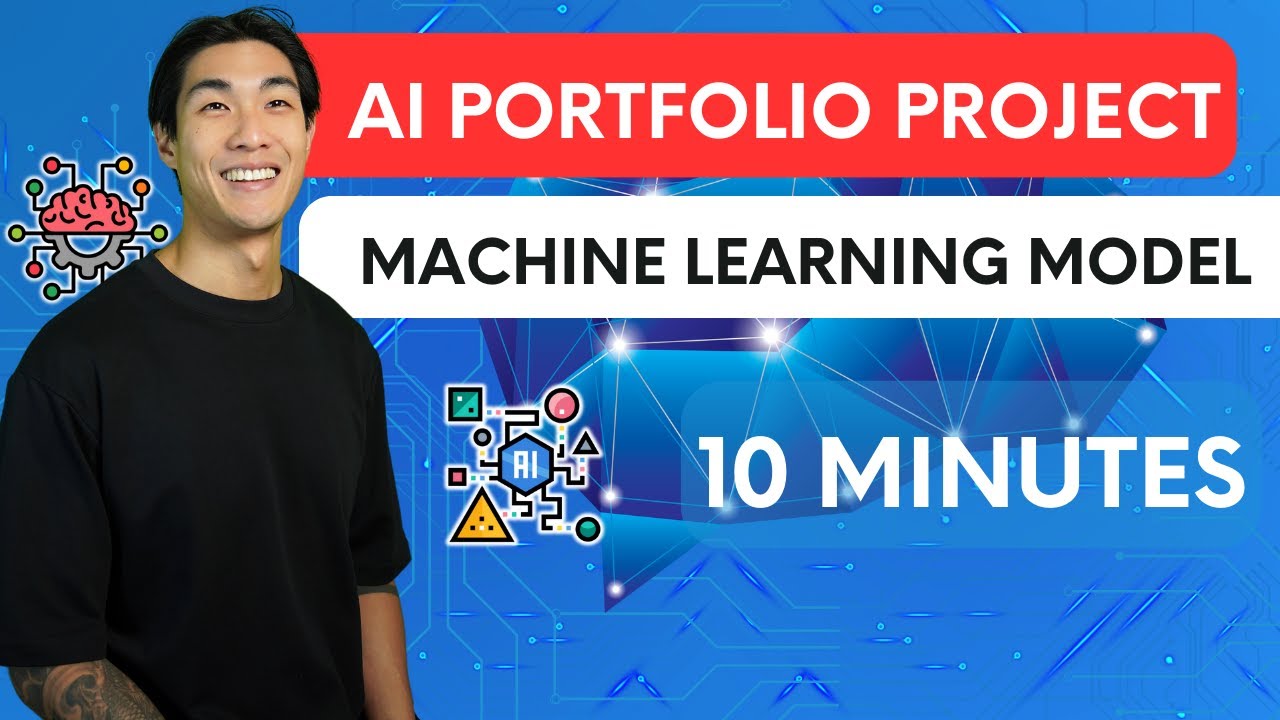
AI Portfolio Project | I built a MACHINE LEARNING MODEL using AI in 10 MINUTES
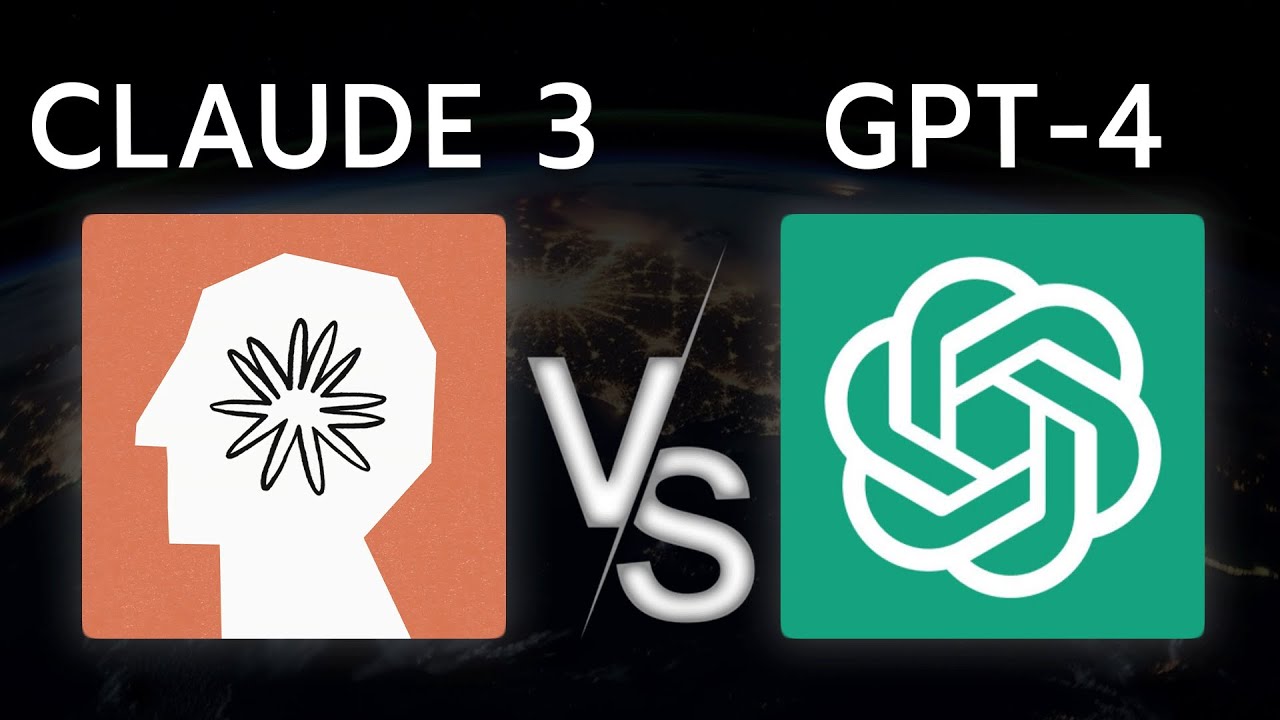
Why & When You Should Use Claude 3 Over ChatGPT
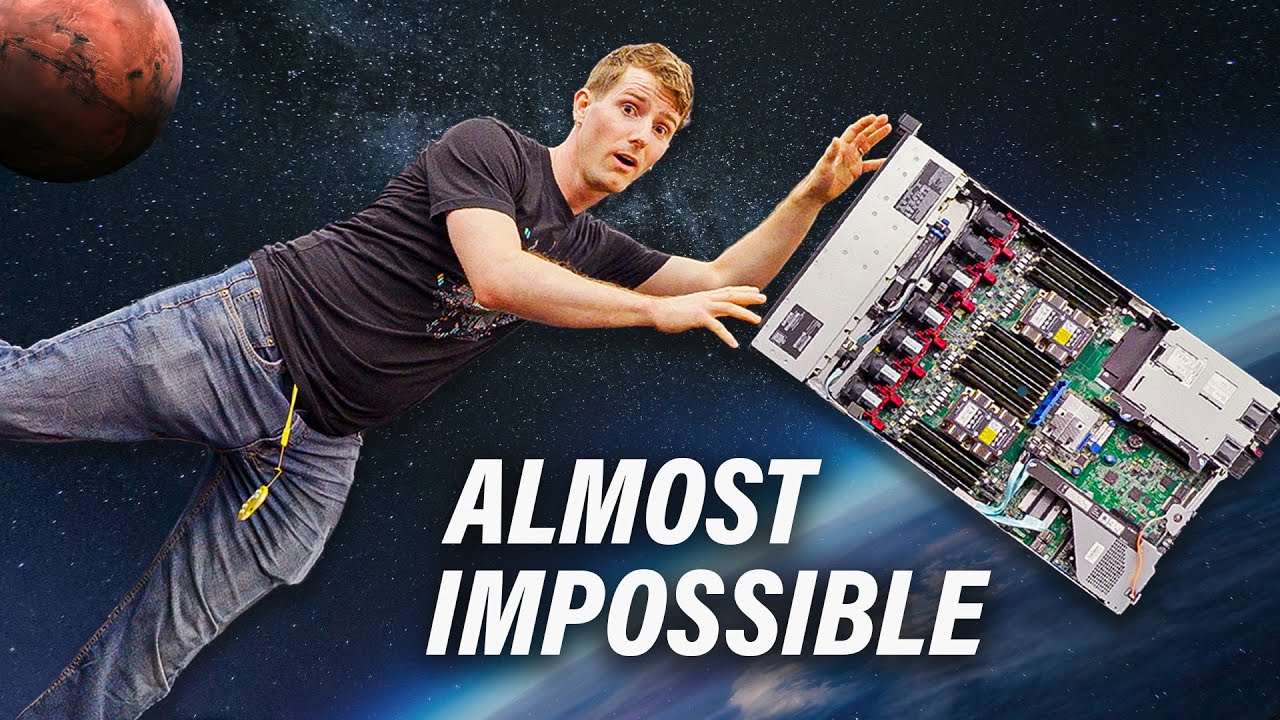
Why it Was Almost Impossible to Put a Computer in Space